Timeline Reference: April 7-14, 2025
Sometimes “good enough” isn’t good enough — especially when you’re building gear that off-roaders trust on real-world trails. This is the story behind why your ARB bracket hasn’t shipped yet — and why that delay is actually a sign of our commitment to getting it right.
⬆️ Decision to Upgrade Mid-Batch
Back in early April, I had a small batch of ARB brackets cut, deburred, and fitted with M6 press-fit studs — ready to move into the next steps. I could have welded them up, sent them off for powder coat, and called it a day.
But I didn’t.
Instead, I made the call to hold off and update those brackets to my latest design, which includes expanded MOLLE mounting capabilities. If you’re going to wait a few extra days, I want you to get the version that earns its keep under the hood — not just the version that was “good enough” a week ago.
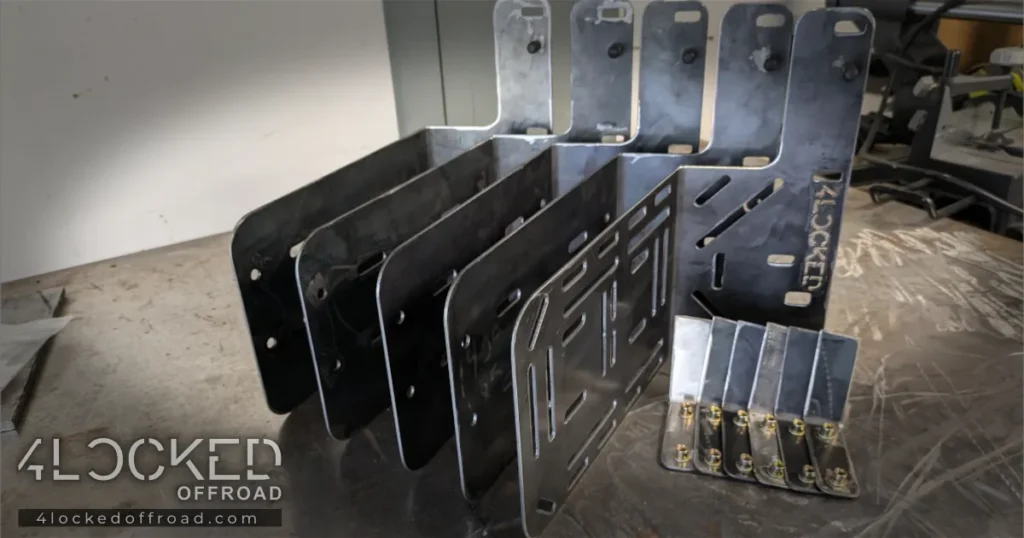
🗜️ First In-House CNC Cuts, First Outsourced Bends
On April 7th, I cut five ARB bracket sets in-house using my Langmuir XR CNC plasma table. This was a milestone — the first time I’d handled cutting in-house.
A couple days later, I dropped those parts off at a local company (let’s call them Company A) for CNC bending. They turned them around fast, and I was optimistic.
But when I got the parts back, I noticed some brackets were underbent by 3–4 degrees. That might not sound like much, but for a precision-fit engine bay bracket, it’s a dealbreaker.
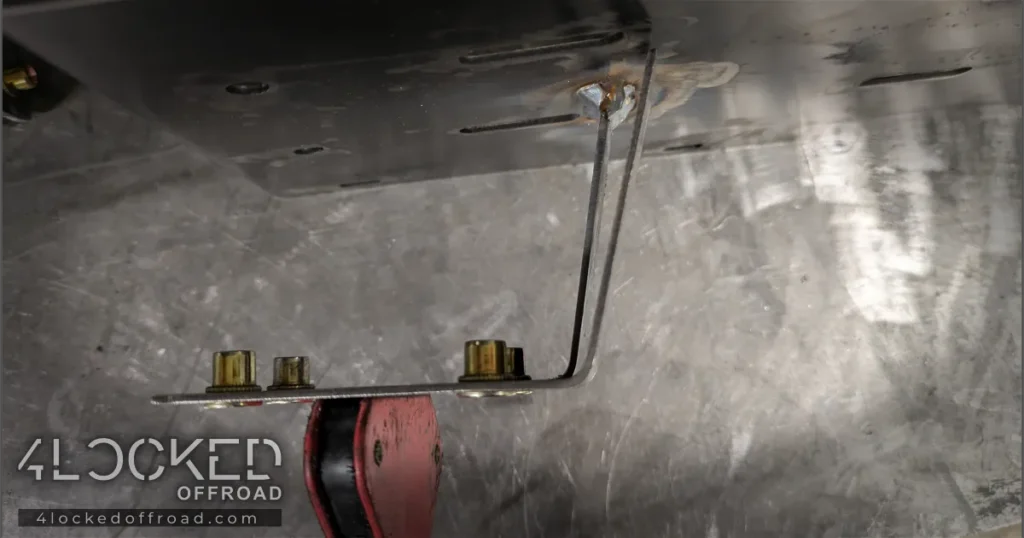
👨🏭 The Welding Wake-Up Call
After getting Company A to re-bend the parts (thankfully they agreed), I attempted to weld them myself. And here’s the truth: my welds weren’t up to the standard I expect for a product I’m sending out the door.
Structurally? Probably fine.
Visually? Not even close.
Rather than settle, I paused again and made the call to outsource welding — but even that came with complications. More on that in Part 2.
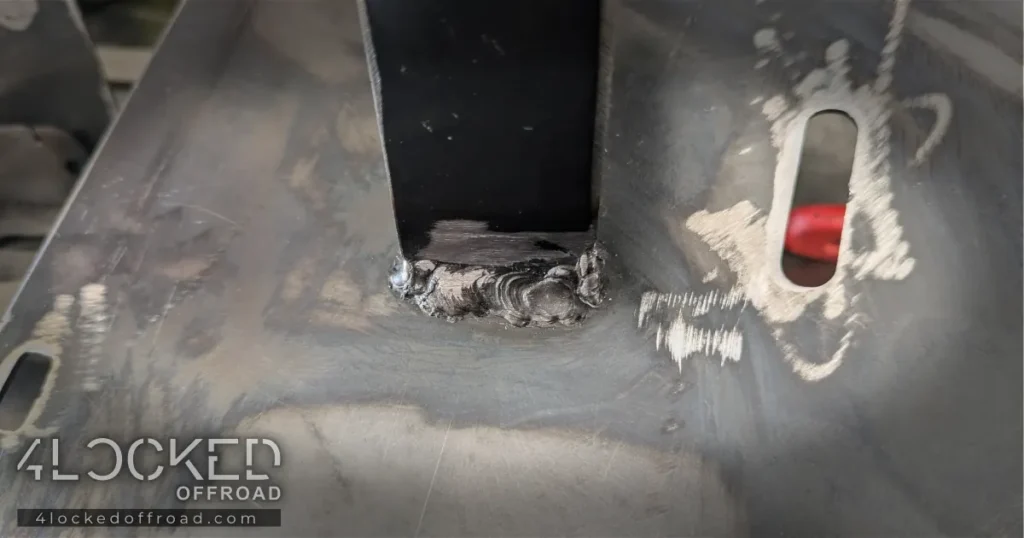
📈 Why This Delay Is a Sign of Progress
I’m a one-man shop building real-world products that go into real-world rigs. That means every delay, every design update, and every setback comes with a lesson — and an opportunity to raise the bar.
You deserve a product that’s built right, not rushed. And this week, that meant scrapping “okay” brackets so you’ll get the best version yet.
Thanks for riding with me — Part 2 drops soon.
⏭️ Coming Up Next in Part 2:
- Tax week chaos
- Welding setbacks
- Why 5 brackets didn’t make it to powder coat
Want more updates like this?
Follow along on our social media or check out the Production News archive.