Timeline Reference: April 21–28, 2025
Sometimes the right path isn’t the easy one. Sometimes it means starting over — with a bigger plan, a better partner, and a commitment to doing it right. Here’s how 18 freshly cut brackets turned a tough setback into a real rebuild — and why even a small material hiccup became a future upgrade opportunity..
🗜️ Recovery in Motion: Cutting 18 New Brackets
By April 21st, it was clear the first small batch of ARB brackets wasn’t going to meet the standards we demand — or that you deserve.
Rather than trying to salvage a compromised batch, I started fresh.
I cut, deburred, and prepared 18 new brackets on the Langmuir XR CNC plasma table, this time incorporating all the latest MOLLE panel mounting upgrades. These weren’t just replacements — they were an evolution.
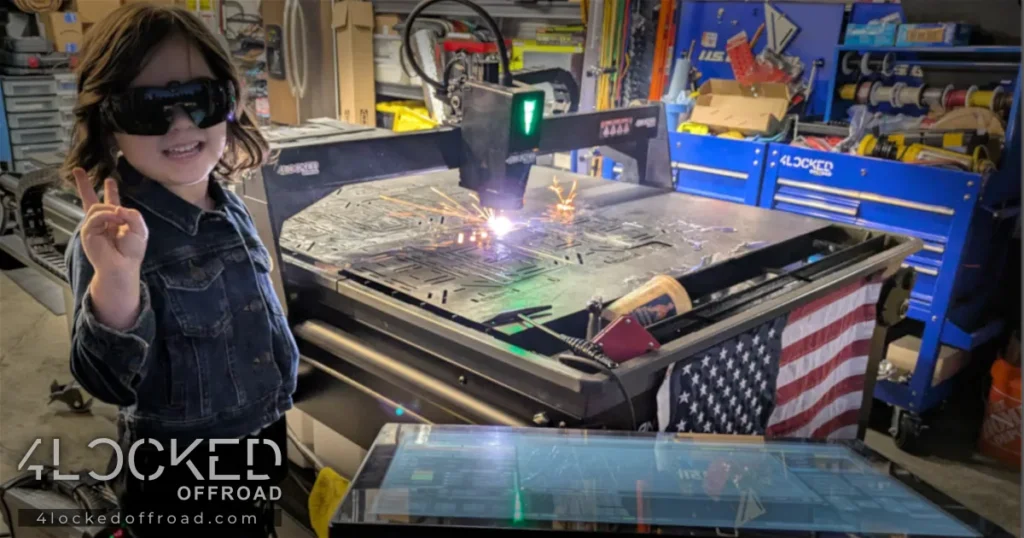
🤝 Building Better Partnerships
On April 22nd, the new batch of bracket parts was dropped off at Company A for CNC bending.
Unfortunately, another hurdle appeared:
While the bend angles were correct, the bend placement was off — causing critical gaps where welded joints needed precision fitment.
It was another blow, but it led to one of the best pivots yet: discovering Company B, a full-service manufacturing shop practically right behind my own shop.
Company B’s capabilities — CNC bending, TIG welding, powder coating, milling, and more — were exactly what 4Locked Offroad needed to control quality, timelines, and future growth.
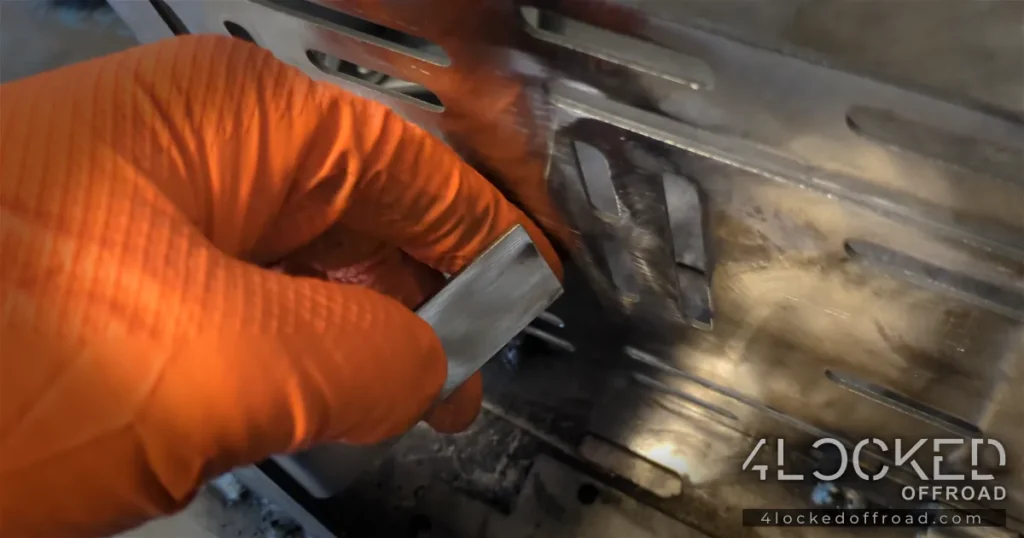
💨 Tactical Recovery: Rapid Adjustments
After realizing the bending problem, I immediately cut out 18 new vertical support pieces, deburred them, and delivered them to Company B on April 24th.
This wasn’t just salvaging the batch — it was pivoting toward a better, stronger production system.
Going forward:
- Company B will handle CNC bending, TIG welding, and powder coating.
- Outsourced dependencies are reduced from three vendors to just one.
- Quality control moves directly into a tighter, more accountable workflow.
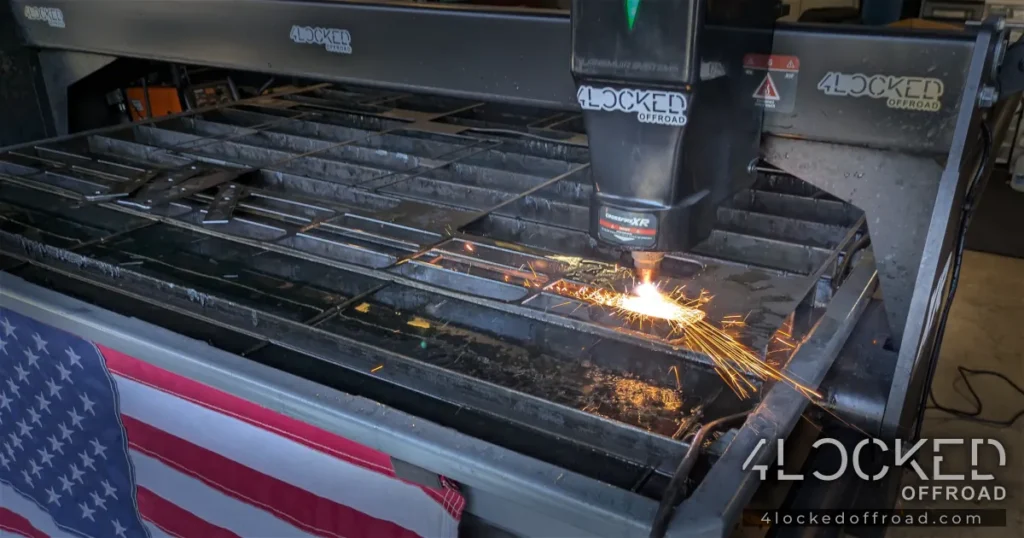
👨🏭 First Welding Test: Confirming the Fit
On April 28th, I visited Company B in person to oversee the first test weld.
Here’s how it went:
- Company B bent a fresh vertical support.
- We installed the rivet nuts immediately.
- Parts were mounted into my custom jig, and TIG welded together under my supervision.
The weld quality was clean, consistent, and strong.
Afterward, I brought the completed test bracket back to my shop and immediately installed it into my own 3rd Gen 4Runner.
Fitment was perfect.
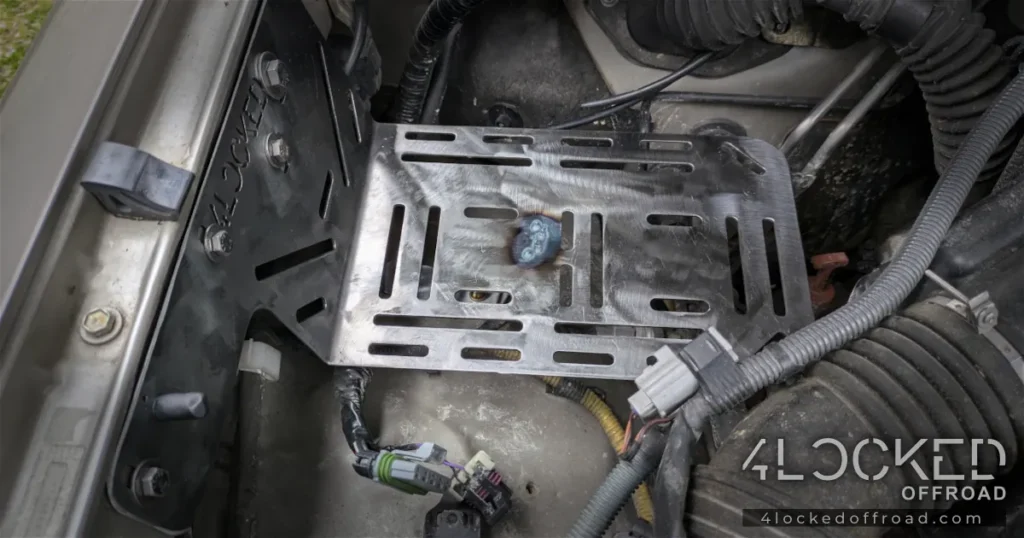
⚙️ A Material Surprise — and a New Opportunity
However, one unexpected discovery surfaced:
This batch was made from 14 gauge mild steel instead of the 11 gauge material previously used.
While 14ga is still rugged and trail-worthy — and strong enough for mounting compressors, fuse panels, and electrical systems — it offers slightly more flex under heavy loads (like an ARB twin compressor).
Rather than scrap the batch, this opened a new opportunity:
Introducing a Future “Duty Rating” Option:
- Light Duty Version (14ga) — lighter weight, strong enough for most installs.
- Heavy Duty Version (11ga) — maximum rigidity for hardcore off-road builds.
Mistakes happen — it’s what you do with them that defines the outcome.
📝 Why This Step Matters
Thanks to close quality control, fast recovery actions, and new vendor partnerships, the bracket project moves forward stronger than ever:
- Reduced outsourced risk — tighter control over manufacturing from here forward.
- Confirmed fitment and TIG weld quality with Company B.
- Future ability to offer Light Duty and Heavy Duty variants.
⏭️ Coming Up Next in Part 4:
- Final TIG welding of full batch
- Powder coating process
- Preparing brackets for final ship-out
Want more updates like this?
Follow along on our social media or check out the Production News archive.