Timeline Reference: April 14–20, 2025
When we wrapped Part 1, the “good enough” brackets were scrapped, and the bar was set higher. But the real battle to finish this batch — and finish it right — had only just begun.
🪙 Tax Week: When Progress Hits Pause
Just as production was ramping back up, tax deadlines hit.
Running a real-world fabrication business means doing real-world paperwork too — and unfortunately, April isn’t just trail season, it’s also tax season.
Hours that could’ve gone to welding, sorting, or finishing brackets were redirected to scanning receipts, updating books, filing taxes, and everything else that keeps the business side of 4Locked Offroad alive.
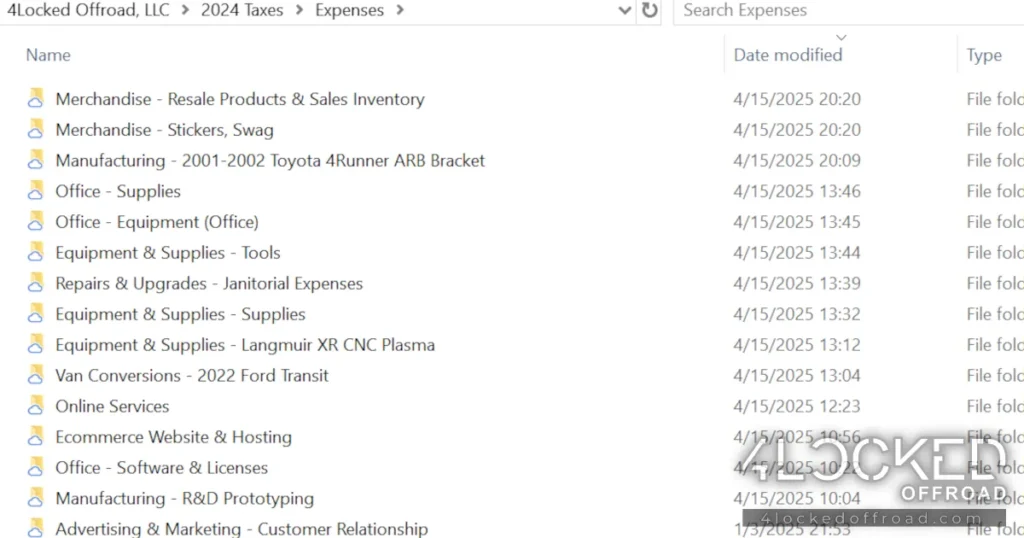
👨🏭 Welding: Outsourced, But Not Out of Trouble
With tax week chaos finally behind me, it was time to get these brackets welded — but after realizing my in-house welds weren’t up to the visual standard I wanted to ship, I made the call to outsource welding.
The goal was simple: clean, strong, professional welds that matched the build quality I expect.
The reality? Not quite.
The welding shop turned the job around fairly quickly — about two days, including a weekend — but when I inspected the parts, I found that almost all the welds had cosmetic flaws.
Here’s a real-world side-by-side showing why “good enough” wasn’t good enough.
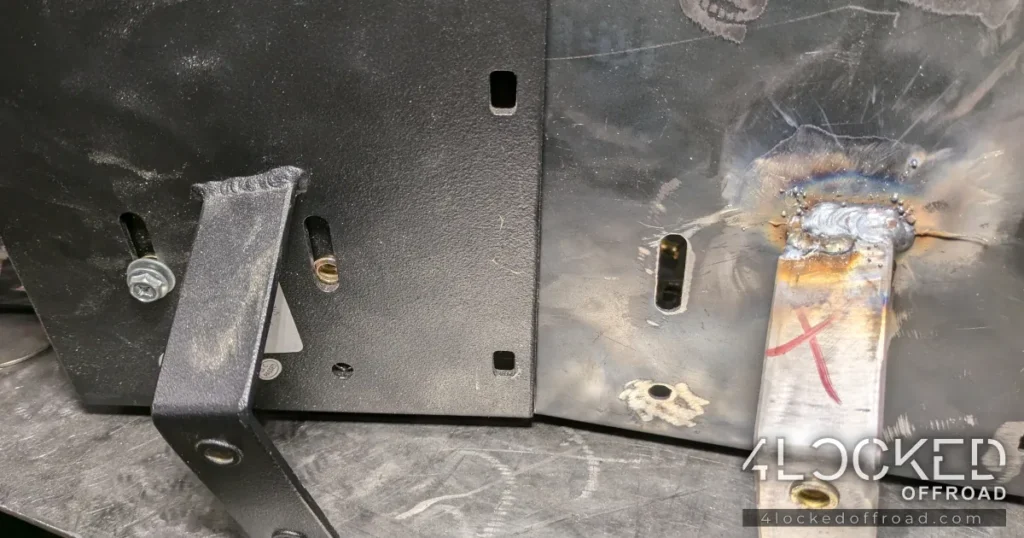
Structurally? They would probably perform fine.
Visually? They weren’t up to the standard I expect to deliver to you.
I had a decision to make: ship them “good enough” — or sort, cull, and protect the 4Locked Offroad name.
🧰 The Final Cull: 5 Brackets Left Behind
Out of the small batch that made it through CNC cutting, bending, stud installation, and outsourced welding — five brackets didn’t make the final cut.
Each one had visual flaws I wouldn’t accept on my own rig — welds that didn’t meet the finish quality you deserve.
In the end, they were pulled aside — not because they were unusable in theory, but because 4Locked Offroad isn’t about “usable enough.”
It’s about trust.
Every bracket that ships has to be something I’m proud to bolt into my own engine bay — and if it doesn’t pass that test, it doesn’t go out the door.
If it’s not right, it doesn’t leave the shop. Simple as that.
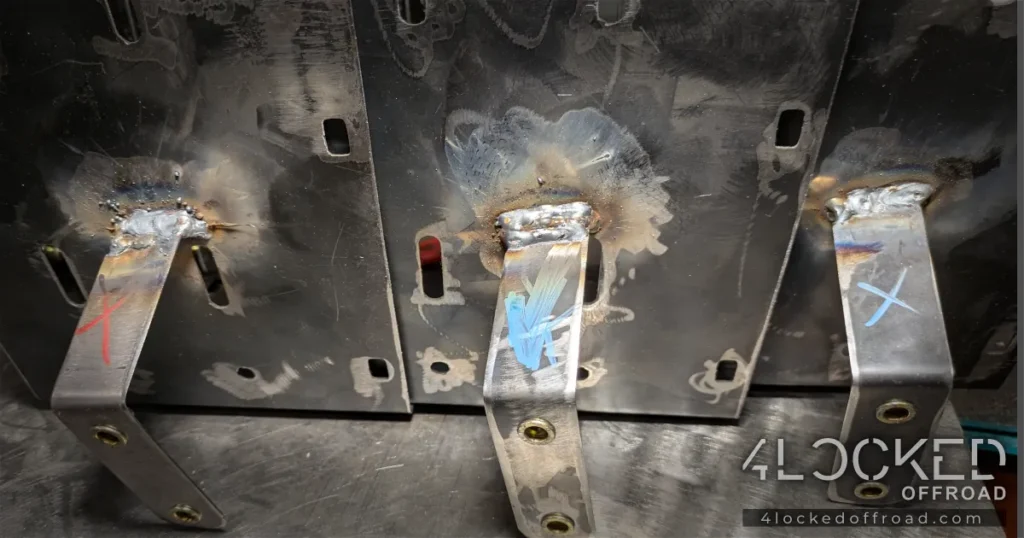
📝 Lessons from the Front Lines
Every bracket scrapped. Every delay accepted. Every tough call made.
That’s what makes the final product something you can depend on — not just to hold an ARB compressor, but to represent the values of real off-roaders building real-world solutions.
Part 2 may have been tough behind the scenes, but it’s one more reason you can trust what’s coming next.
⏭️ Coming Up Next in Part 3:
- Cutting and prepping a full new batch of 18 brackets
- Discovering a serious bending error (again)
- Establishing a promising new manufacturing partnership
Growth isn’t just about wins — it’s about learning who you can trust to build with. See what’s next in Part 3.
Want more updates like this?
Follow along on our social media or check out the Production News archive.